Ta strona korzysta z ciasteczek, aby zapewnić Ci najlepszą możliwą obsługę. Informacje o ciasteczkach są przechowywane w przeglądarce i wykonują funkcje takie jak rozpoznawanie Cię po powrocie na naszą stronę internetową i pomaganie naszemu zespołowi w zrozumieniu, które sekcje witryny są dla Ciebie najbardziej interesujące i przydatne.
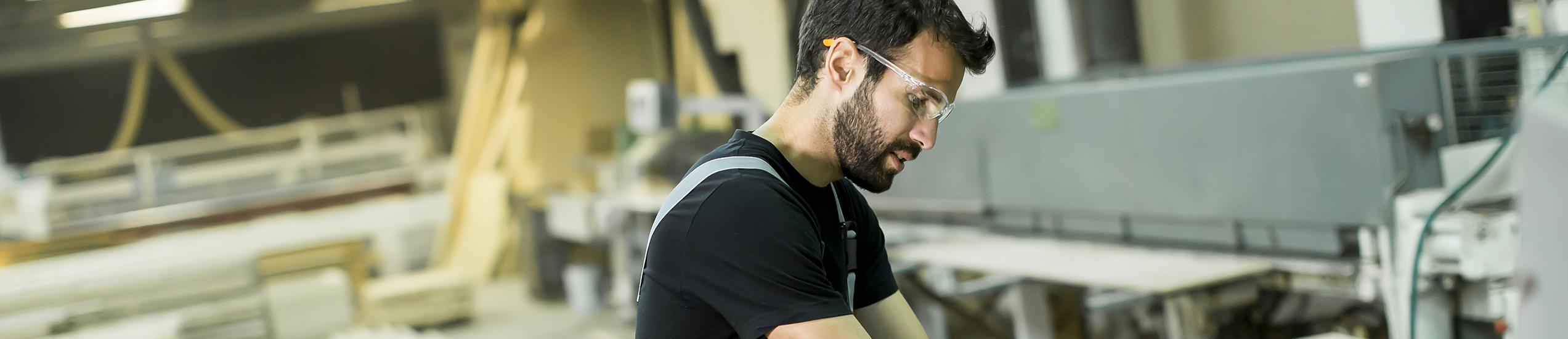
Klient
Steinemann Technology AG to globalny lider w produkcji maszyn szlifierskich do płyt drewnianych oraz systemów lakierowania UV dla przemysłu graficznego. Firma od ponad wieku dostarcza innowacyjne rozwiązania, które napędzają rozwój branży produkcyjnej. W obliczu rosnących wymagań operacyjnych i technologicznych Steinemann stanął przed koniecznością modernizacji swojego systemu sterowania maszynami, który nie spełniał już współczesnych standardów UX i ograniczał efektywność produkcji. Klient szukał rozwiązania, które nie tylko wyeliminuje dotychczasowe ograniczenia, ale także stworzy fundament pod przyszłą cyfryzację i usprawnienie procesów produkcyjnych.
Wyzwanie
Celem projektu była budowa nowego systemu do automatyzacji procesu szlifowania. Nowe rozwiązanie miało poprawić wydajność produkcji, zwiększyć modularność, obniżyć koszty utrzymania oraz zapewnić lepszą kontrolę jakości w warunkach fabrycznych.
Steinemann zwrócił się do nas z prośbą o opracowanie wizji ewolucji swojego oprogramowania i kompleksowe wdrożenie nowego systemu zgodnie z najlepszymi praktykami. Projekt realizowaliśmy w ścisłej współpracy z klientem, co umożliwiło bieżące doprecyzowanie wymagań, szybką komunikację o ryzykach oraz wspólne wypracowywanie optymalnych rozwiązań.
W Steinemann podstawą działalności jest precyzja, efektywność i powtarzalne efekty. Jednak dotychczasowy system zarządzania jakością produkcji płyt stał się barierą w dalszym rozwoju.
Największe problemy obejmowały:
- Dane z czujników i maszyn były przetwarzane synchronicznie z dużymi opóźnieniami – zmiany w parametrach procesu pojawiały się na interfejsie nawet z 10-sekundowym opóźnieniem. W praktyce uniemożliwiało to operatorom podejmowanie decyzji na bieżąco, bo zanim zauważyli problem na ekranie, produkt mógł już zostać wadliwie obrobiony.
- Brak zdalnego dostępu i ograniczenia w monitoringu — system zarządzania jakością płyt działał tylko lokalnie na maszynach, a dział IT nie miał możliwości zdalnego wglądu w pracę urządzeń. Brak centralnego dostępu utrudniał diagnozowanie awarii, z kolei brak logów zdarzeń uniemożliwiał analizę problemów.
- Skomplikowany interfejs użytkownika – operatorzy musieli przechodzić długie szkolenia, aby efektywnie korzystać z systemu, a sama obsługa wymagała wielu manualnych kroków.
- Trudności w utrzymaniu i rozwoju systemu – wprowadzanie zmian i nowych funkcji było czasochłonne i kosztowne. Modyfikacja pojedynczego przycisku mogła trwać nawet kilka miesięcy. Z kolei brak modularności wymuszał ingerencję w całą aplikację, a każda aktualizacja wiązała się z ryzykiem nowych błędów.
Steinemann potrzebował nowoczesnego rozwiązania, które zwiększy efektywność operacyjną, poprawi komfort pracy operatorów i umożliwi łatwą rozbudowę systemu w przyszłości.
Nasze rozwiązanie
Aby sprostać oczekiwaniom klienta, zaproponowaliśmy stworzenie nowego systemu zarządzania jakością płyt od podstaw – zaprojektowanego z myślą o nowoczesnej architekturze, wysokiej dostępności danych i intuicyjnej obsłudze. Najważniejsze decyzje projektowe objęły wybór architektury modułowej opartej na kontenerach (Docker) oraz integrację z istniejącą infrastrukturą przemysłową klienta. Nowy system BQC Automation został zaprojektowany jako stabilne, niezawodne rozwiązanie kontenerowe, które łatwo wdrażać i aktualizować na wielu maszynach jednocześnie. Dzięki konteneryzacji przyszłe aktualizacje oprogramowania mogą być przeprowadzane płynnie (praktycznie bez przestojów), co znacząco skraca czas dostarczania poprawek i nowych funkcji w porównaniu do starego systemu.
Architektura systemu oparta o OPC Connector
OPC Connector to moduł pośredniczący, który komunikuje się z maszynami i czujnikami na hali. OPC zbiera w czasie rzeczywistym dane procesowe (np. prędkości rolek, pobór prądu, grubość szlifowanych płyt), przetwarza je i w razie potrzeby wysyła komendy zwrotne do urządzeń sterujących. Umożliwia to zamknięcie pętli sterowania – system może automatycznie dostosować parametry pracy maszyny, aby utrzymać stabilną jakość produkcji.
Opracowaliśmy specjalny algorytm kontroli jakości szlifowania, który na podstawie danych z czujników reguluje obciążenie maszyny w czasie rzeczywistym, zapobiegając jej przemęczeniu i gwarantując powtarzalną jakość każdej płyty.
Dzięki nowej architekturze wszystkie dane produkcyjne są dostępne natychmiast – zredukowaliśmy opóźnienie odczytu parametrów do <100 ms, co w praktyce oznacza, że praca odbywa się w czasie rzeczywistym. Poprzedni system odświeżał dane co ok. 10 sekund. Tak wyraźna poprawa responsywności była możliwa m.in. dzięki wyodrębnieniu dedykowanego konektora OPC – oddzielnej warstwy komunikacji z maszyną, co usprawniło przesył danych (wcześniej obsługa OPC była „zaszyta” w kodzie starej aplikacji i działała nieefektywnie).
Nowy interfejs użytkownika
Dużą wagę przywiązaliśmy do nowego interfejsu użytkownika. Naszym celem było stworzenie systemu zarządzania jakością szlifowania maksymalnie przyjaznego operatorom maszyn, który przyczyni się do wzrostu produktywności i zmniejszy częstotliwość popełniania błędów przez obsługę.
W tym zakresie przeprowadziliśmy analizę UX istniejącego rozwiązania wraz z klientem i na tej podstawie podjęliśmy kilka ważnych decyzji projektowych:
- Uproszczenie interfejsu — nowa aplikacja zawiera tylko niezbędne funkcje, a układ ekranów został przebudowany tak, by odciążyć poznawczo użytkownika i ułatwić nawigację. Wyeliminowano zbędne kroki i informacje, które rozpraszały operatorów w poprzednim systemie.
- Intuicyjność — zastosowaliśmy nowoczesne wzorce projektowania UX/UI, dzięki czemu obsługa systemu jest bardziej intuicyjna i spójna z oczekiwaniami użytkowników przyzwyczajonych do współczesnych aplikacji. Elementy sterujące są logicznie pogrupowane, a alerty i komunikaty formułowane w zrozumiały sposób. To wszystko skraca czas potrzebny na przeszkolenie nowych operatorów.
- Personalizacja i elastyczność — nowe oprogramowanie zostało zaprojektowane modułowo, co umożliwia dostosowanie funkcji do potrzeb konkretnej fabryki. W razie potrzeby do podstawowego systemu można dodawać dodatkowe moduły (add-ons) bez modyfikacji rdzenia aplikacji.
- Administratorzy mają teraz możliwość konfiguracji uprawnień i interfejsu dla różnych ról użytkowników (np. operator, inżynier, menedżer) – dzięki temu każdy widzi tylko te funkcje, których potrzebuje.
- System udostępnia również webowy interfejs dostępny przez przeglądarkę (Chrome, Firefox, Edge). Można go uruchomić na dowolnym komputerze lub tablecie w sieci zakładowej, bez konieczności instalacji dedykowanego oprogramowania na każdej maszynie. Jest to interfejs responsywny i dostosowany do trudnych warunków produkcyjnych (np. czytelny na dużych ekranach w hali).
Nowe rozwiązanie zostało przystosowane do pracy w szerszym ekosystemie
System komunikuje się nie tylko z maszynami poprzez OPC, ale także z zewnętrznymi platformami, takimi jak chmura Azure klienta. Dane produkcyjne mogą być wysyłane do chmury, co otwiera drogę do zdalnego nadzoru, skalowalności infrastruktury oraz analizy danych w celu dalszej optymalizacji. Zadbaliśmy również o mechanizmy bezpieczeństwa i niezawodności. System posiada lokalny bufor danych na wypadek utraty połączenia z siecią. Dzięki temu nawet przy awarii łącza internetowego praca maszyny i zbieranie danych jakościowych nie zostaną przerwane.
Sprawdzona metodologia 4D
Biorąc pod uwagę złożoność projektu i cele biznesowe klienta, zdecydowaliśmy się zastosować naszą sprawdzoną metodologię 4D (Discovery, Definition, Delivery, Direction), wspartą podejściem Agile i technikami Design Thinking. Taki model pracy umożliwił iteracyjne dostarczanie rezultatów przy stałej kontroli jakości i ryzyk.
- W fazie Discovery skupiliśmy się na pełnym zrozumieniu potrzeb użytkowników i problemów, jakie mamy rozwiązać – m.in. poprzez warsztaty z udziałem inżynierów Steinemann, analizę procesu szlifowania oraz badanie istniejącego systemu do zarządzania jakością szlifowania.
- Następnie, w fazie Definition dopracowaliśmy wymagania (funkcjonalne i niefunkcjonalne), przygotowaliśmy koncepcje UX oraz zaprojektowaliśmy docelową architekturę systemu. Dzięki szybkiemu prototypowaniu byliśmy w stanie wcześnie zweryfikować z klientem najważniejsze założenia i wprowadzić niezbędne korekty przed właściwą implementacją.
- W fazie Delivery jednym z największych wyzwań technicznych okazała się integracja z maszyną poprzez OPC. Opracowanie niezawodnego konektora wymagało ścisłej współpracy naszych programistów z inżynierami klienta, jednak finalnie udało się osiągnąć stabilne, szybkie połączenie. Równolegle dopracowywaliśmy algorytm automatycznej kontroli jakości szlifowania, który wymagał walidacji w warunkach produkcyjnych. W tym celu nasz zespół dwukrotnie odwiedził zakład klienta i przeprowadził testy bezpośrednio na liniach produkcyjnych. Testowanie „na żywo” dało pewność, że opracowane rozwiązanie działa zgodnie z założeniami i faktycznie poprawia jakość wyrobów. Ostatnie dwa tygodnie projektu przeznaczyliśmy wyłącznie na testy systemu – zarówno automatyczne, jak i manualne, w tym testy akceptacyjne z udziałem przyszłych użytkowników. Dzięki temu mogliśmy wychwycić i wyeliminować drobne usterki przed wdrożeniem produkcyjnym.
- Faza Direction, czyli wdrożenie i wsparcie po wdrożeniowe. Po zakończeniu prac deweloperskich przeprowadziliśmy szkolenia operatorów oraz asystowaliśmy przy uruchomieniu systemu na pierwszej linii produkcyjnej. Nowy system zarządzania jakością szlifowania został wdrożony równolegle z istniejącym systemem (na zasadzie pilotażu) w celu bezpiecznego porównania działania. Operatorzy bardzo pozytywnie ocenili nowy interfejs, który okazał się przejrzysty i łatwy w obsłudze, co potwierdziło wcześniejsze założenia o skróceniu czasu nauki obsługi maszyny. Przez pierwsze tygodnie po wdrożeniu nasz zespół zapewniał bieżące wsparcie takie jak np. zdalne monitorowanie systemu czy szybką reakcję na pytania użytkowników. Po fazie rozruchu pilotażowego klient zdecydował o stopniowym wdrażaniu nowego systemu zarządzania jakością szlifowania na pozostałych maszynach i liniach produkcyjnych. Na koniec przekazaliśmy Steinemann komplet dokumentacji powykonawczej oraz rekomendacje dotyczące dalszego rozwoju systemu.
Rezultaty
Wdrożenie nowego systemu usprawniło codzienną pracę operatorów, a także ogólne zarządzanie procesem produkcji.
Klient uzyskał znaczną poprawę efektywności i jakości procesu szlifowania płyt. Dzięki automatyzacji kontroli jakości maszyna na bieżąco koryguje parametry pracy, co przełożyło się na bardziej jednolite pod kątem jakości produkty i ograniczenie liczby odrzutów.
Operatorzy zyskali wgląd do procesu w czasie rzeczywistym. Kluczowe dane i wskaźniki są dostępne od razu na czytelnych dashboardach. Wyeliminowaliśmy problem opóźnień danych. Decyzje operacyjne mogą być podejmowane natychmiast, a system generuje automatyczne alerty, gdy tylko wykryje nieprawidłowość.
Nowy interfejs użytkownika jest przyjazny i intuicyjny. Czas szkolenia nowych pracowników został zredukowany z kilku dni do zaledwie kilku godzin.
Dzięki modułowej budowie i elastycznej konfiguracji ról system lepiej wspiera współpracę różnych działów. Operatorzy koncentrują się na swoich zadaniach, a inżynierowie procesu czy menedżerowie produkcji mają dostęp do bardziej zaawansowanych analiz bez ingerowania w pracę operatorów.
Ujednolicenie środowiska systemu zarządzania jakością szlifowania pozwoliło zastąpić wiele rozproszonych stanowisk jednym scentralizowanym systemem. Zamiast utrzymywać kilka osobnych ekranów i komputerów dla każdej maszyny, wystarczy teraz standardowy terminal z przeglądarką internetową. To z kolei przekłada się na niższe koszty sprzętu i utrzymania. Modernizacja oprogramowania wydłużyła także cykl życia maszyn – dzięki ciągłemu monitorowaniu ich stanu i automatycznym korektom obciążenia maszyny są mniej narażone na awarie spowodowane niewłaściwymi ustawieniami.
Cała inwestycja stworzyła solidną bazę pod przyszłe usprawnienia. Firma Steinemann zyskała nowoczesną platformę, którą w kolejnych etapach można rozwijać o nowe funkcje takie jak np. zaawansowaną analitykę danych produkcyjnych, mechanizmy predykcyjnej konserwacji czy integrację z innymi systemami w fabryce.
Technologie
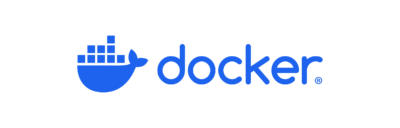
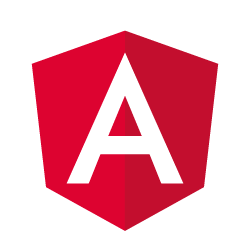
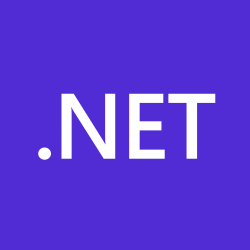
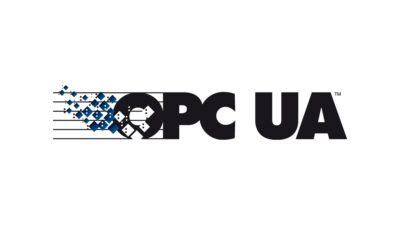
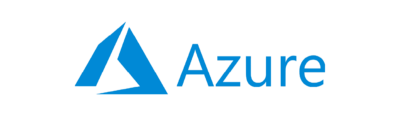
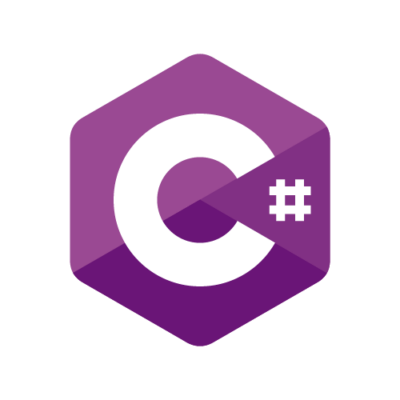
Klient
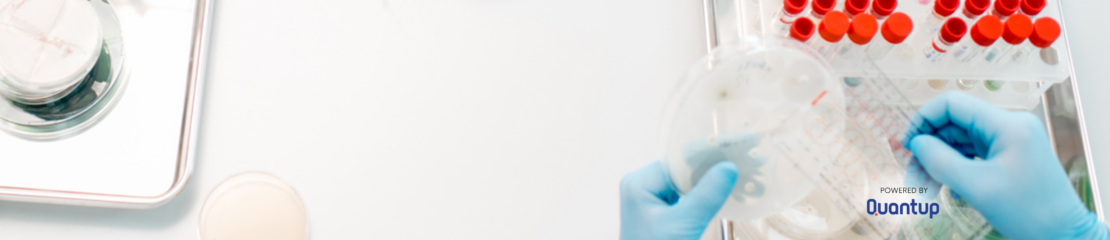
Design, Development, DevOps czy Cloud – jakiego zespołu potrzebujesz, aby przyspieszyć pracę nad swoimi projektami?
Porozmawiaj o swoich potrzebach z naszymi specjalistami.
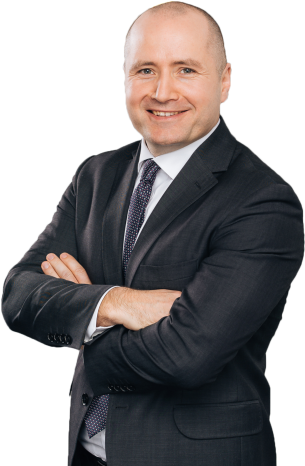