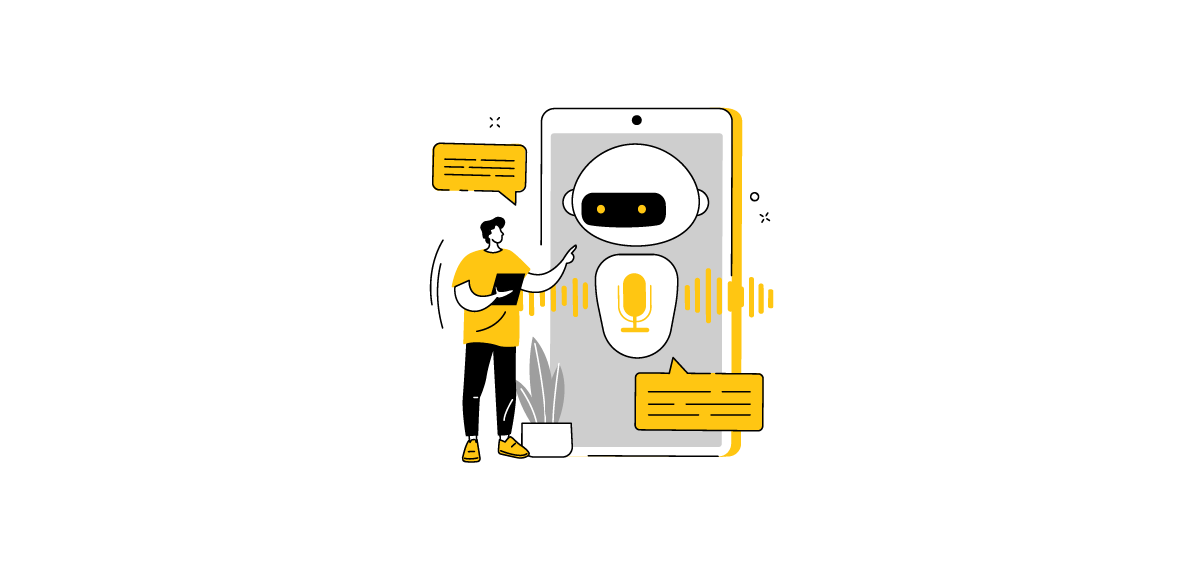
Przetwarzanie danych w środowisku produkcyjnym wiąże się z wieloma wyzwaniami. W tym artykule pokazujemy, jak OPC Gateway optymalizuje izolowane przechowywanie danych, integrację starszych maszyn oraz dostęp do danych w czasie rzeczywistym. Wyjaśniamy technologię, przepływ danych z hali produkcyjnej do chmury oraz przykłady zastosowania w cyfryzacji hali produkcyjnej. Przyglądamy się również roli OPC Gateway w analizie danych w czasie rzeczywistym, optymalizacji procesów i trwałej implementacji. Na koniec omawiamy przyszłość standardu OPC UA i Industrial IoT.
Spis treści
Definicja i rola: Czym jest OPC Gateway i jakie ma znaczenie w połączonej produkcji?
OPC Gateway to narzędzie oparte na protokole OPC UA, który jest jednym z kluczowych standardów komunikacyjnych dla Przemysłu 4.0. Jest to standard niezależny od platformy, zapewniający bezpieczną i niezawodną wymianę danych w środowisku przemysłowym. Dane są zbierane z różnych źródeł i analizowane centralnie. Zanim jednak do tego dojdzie, konieczne jest przetłumaczenie różnych protokołów komunikacyjnych na wspólny język, umożliwiający jednolite przetwarzanie danych. Jedną z głównych zalet tego systemu jest możliwość działania w czasie rzeczywistym – oznacza to natychmiastowe przetwarzanie i przesyłanie danych. Jest to ogromna zaleta, ponieważ eliminuje tzw. silosy danych, czyli izolowane przechowywanie danych.
W poniższej tabeli zestawiliśmy kluczowe aspekty OPC Gateway i podkreśliliśmy jego najważniejsze zalety:
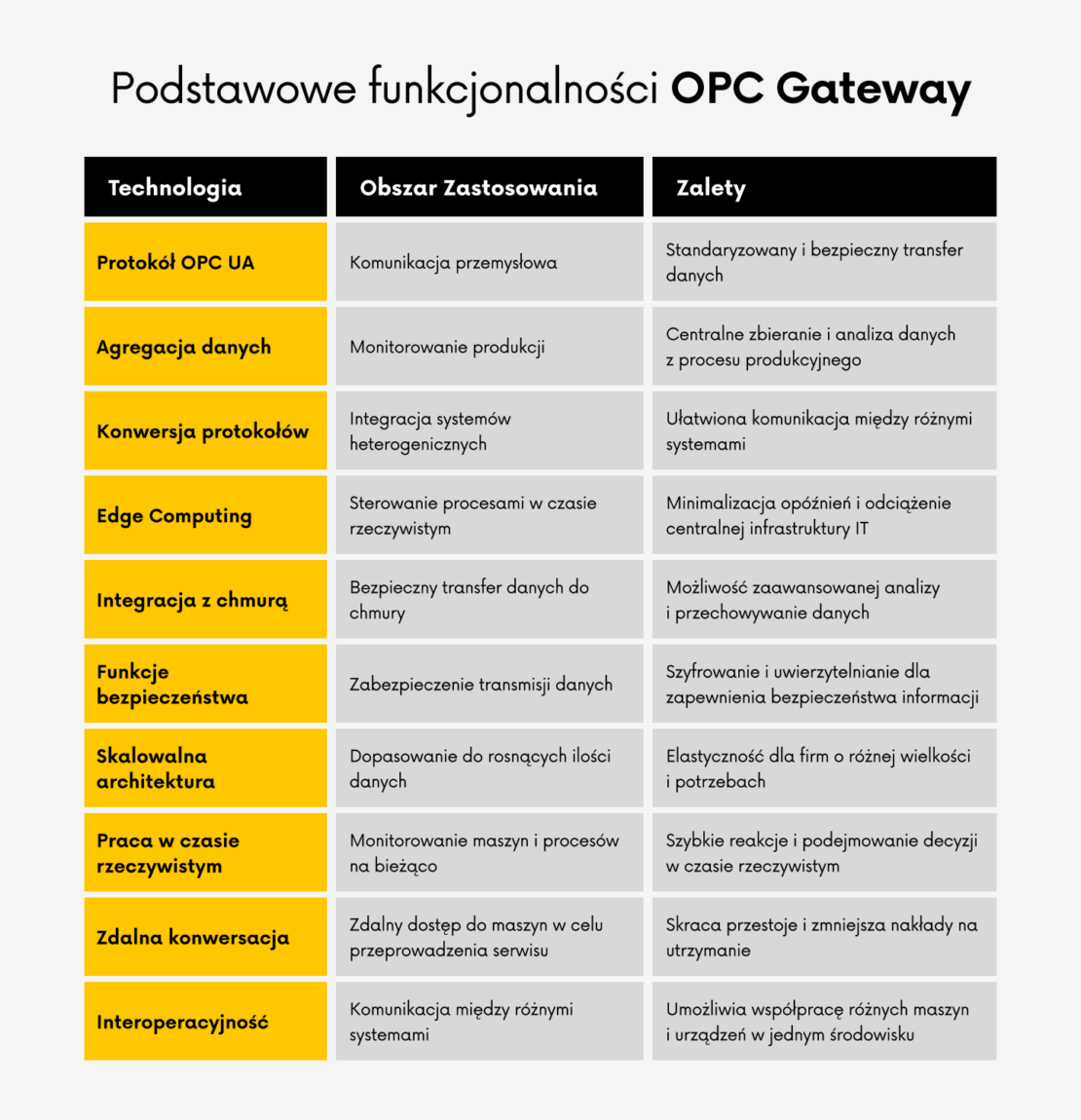
Przepływ danych z hali produkcyjnej do chmury: płynna integracja z nowoczesnymi systemami
OPC Gateway skutecznie integruje dane produkcyjne z nadrzędnymi systemami, przesyłając je w czasie rzeczywistym do chmury, z jednoczesną obsługą starszych systemów. Do komunikacji wykorzystywane są standardowe protokoły, takie jak OPC UA, które umożliwiają integrację maszyn i systemów różnych producentów. Dane produkcyjne są ujednolicane i analizowane za pomocą usług chmurowych.
Chmura daje możliwość dostępu do danych z dowolnego miejsca i o każdej porze, a także ich wykorzystania do wszelkiego rodzaju analiz. Aby zapewnić stałą dostępność informacji, OPC Gateway automatycznie synchronizuje dane. Pozyskane informacje mogą być analizowane i w przejrzysty sposób prezentowane za pomocą narzędzi do wizualizacji danych.
Wszystkie te dane wspierają optymalizację planowania produkcji – obejmującą m.in. okna serwisowe, zaopatrzenie w materiały i zarządzanie zasobami produkcyjnymi.
Wyzwania integracji danych: Dlaczego tradycyjne podejścia zawodzą
Stare maszyny i brak interfejsów: Fabryki borykają się z wieloma problemami związanymi z podłączeniem do nowoczesnych technologii. Stare maszyny często nie posiadają nowoczesnych interfejsów do transmisji danych. OPC Gateway potrafi w takich przypadkach „dodać” brakujący interfejs, umożliwiając przepływ danych do nowoczesnych systemów. W porównaniu do zakupu nowych maszyn ze wbudowanymi interfejsami jest to bardzo korzystne rozwiązanie ekonomiczne.
Systemy heterogeniczne: To kolejna duża przeszkoda w wielu przedsiębiorstwach – czyli równoległe funkcjonowanie różnych systemów, które nie potrafią się ze sobą komunikować. OPC Gateway rozwiązuje ten problem poprzez tłumaczenie danych z różnych systemów na wspólny język, umożliwiając ich płynną i jednolitą komunikację w ramach jednego standardu.
Brak danych w czasie rzeczywistym: OPC Gateway umożliwia przesyłanie danych produkcyjnych w czasie rzeczywistym, co wcześniej było możliwe jedynie z opóźnieniem. Dzięki temu decyzje mogą być podejmowane znacznie szybciej i precyzyjniej.
Inne problemy: OPC Gateway pomaga także w przypadkach niskiej jakości danych – dzięki standaryzowanej metodzie ich pozyskiwania i agregacji – oraz przy skomplikowanej integracji systemów i wielu innych wyzwaniach związanych z digitalizacją produkcji.
Analiza w czasie rzeczywistym i optymalizacja procesów: rola OPC Gateway
OPC Gateway oferuje szereg możliwości, które przyspieszają podejmowanie decyzji opartych na danych i redukują przestoje w produkcji.
Poniżej przedstawiamy 10 najważniejszych przykładów zastosowania:
- Monitorowanie procesów
OPC Gateway nadzoruje wszystkie procesy produkcyjne w czasie rzeczywistym, wykrywając nieefektywności na wczesnym etapie. - Predykcyjne utrzymanie ruchu (Predictive Maintenance)
Dzięki ciągłej analizie danych z maszyn można z wyprzedzeniem wykrywać potrzeby konserwacyjne i planować prace serwisowe w taki sposób, aby nie zakłócały procesu produkcyjnego. - Optymalizacja wydajności produkcji
Na podstawie zebranych danych OPC Gateway identyfikuje wąskie gardła i umożliwia działania korygujące, co w konsekwencji prowadzi do zwiększenia wydajności produkcji. - Wykrywanie błędów i kontrola jakości
W przypadku nieprawidłowości w procesie produkcyjnym system natychmiast je identyfikuje i podejmuje działania naprawcze, co pozwala utrzymać wysoką jakość produktów. - Podejmowanie decyzji opartych na danych
Dzięki monitorowaniu wszystkich istotnych systemów w czasie rzeczywistym decyzje można podejmować szybko i na podstawie wiarygodnych informacji. - Optymalizacja zużycia energii
Dane zbierane przez OPC Gateway mogą być wykorzystane do analizy i redukcji zużycia energii, co prowadzi do obniżenia kosztów energetycznych. - Usprawniona komunikacja
Integracja danych z różnych źródeł poprawia przepływ informacji pomiędzy poszczególnymi działami produkcyjnymi, zwiększając spójność działania. - Redukcja przestojów
Dzięki predykcyjnej konserwacji maszyn możliwe jest nie tylko zoptymalizowanie procesów, ale także znaczące ograniczenie przestojów produkcyjnych. - Zwiększenie elastyczności
W przypadku zmian rynkowych system może szybko dostosować procesy produkcyjne do nowych wymagań, co zwiększa konkurencyjność firmy. - Zwiększenie przejrzystości
Ponieważ wszystkie dane produkcyjne są dostępne dla pracowników w czasie rzeczywistym, zapewniona jest pełna transparentność w całym przedsiębiorstwie.
Dobre praktyki wdrażania i obsługi OPC Gateway
Bezpieczeństwo sieciowe oraz skalowalność to kluczowe zagadnienia we współczesnych rozwiązaniach IT. Dlatego istotne jest, aby…
… do przesyłania danych między maszynami wykorzystywane były technologie szyfrowania, takie jak TLS/SSL.
… dostęp do określonych danych miały wyłącznie osoby uprawnione, dzięki odpowiednio zdefiniowanym prawom dostępu.
… integralność danych była zapewniana poprzez sumy kontrolne i algorytmy skrótu (hash), co gwarantuje nienaruszalność danych podczas ich przesyłania.
… wdrożone były systemy redundantne i mechanizmy tworzenia kopii zapasowych, aby zapobiegać utracie danych.
… chmura była wykorzystywana do skalowania architektury OPC Gateway, co pozwala elastycznie rozszerzać system w miarę wzrostu ilości przetwarzanych danych.
Inne istotne kwestie w tym kontekście to monitorowanie i system alarmowy, automatyczne aktualizacje oprogramowania, integracja z zaporą sieciową (firewallem) oraz unikanie tzw. pojedynczych punktów awarii (Single Points of Failure).
Perspektywy na przyszłość: OPC UA, Industrial IoT i fabryki nowej generacji
Wszystkie wskazuje na to, że w nadchodzących latach możemy spodziewać się znaczących udoskonaleń w istniejących technologiach, jak również pojawienia się nowych rozwiązań. Dzięki technologii 5G transmisja danych w czasie rzeczywistym stanie się jeszcze szybsza, sztuczna inteligencja będzie dokładniej prognozować oraz efektywniej wprowadzać optymalizacje. Wzrośnie również poziom autonomii maszyn i systemów, a OPC Gateway będą pełnić funkcję mostu komunikacyjnego. Również w obszarze Industrial IoT (IoT) OPC Gateway odegra jeszcze bardziej znaczącą rolę, zapewniając płynną komunikację między maszynami i systemami.
Warto więc jak najszybciej wejść w ten dynamicznie rozwijający się obszar, który już dziś, a tym bardziej w przyszłości, stanie się standardem w zakresie optymalizacji przepustowości produkcyjnej i procesów.
Szczegółowe informacje na ten temat można znaleźć w naszym case study, w którym opisujemy wdrożenie OPC Gateway u jednego z naszych klientów. Dowiedzą się m.in., w jaki sposób rejestrujemy dane z czujników, wdrażamy komunikację asynchroniczną i świadczymy usługi zdalnego serwisowania oprogramowania – bez konieczności obecności na miejscu lub łączenia się za pomocą TeamViewer.